Best Practices for Excavation on Complex Projects
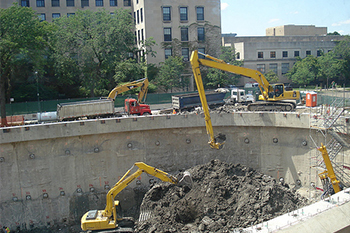
When you specialize in complex commercial and industrial excavation projects, difficult settings are not really the exception. They’re what you face every day. Decades of experience are essential for managing complex excavation settings and challenging ground conditions.
But experience is only part of the reason JKC is successful at managing tough jobs. A bigger part is approaching every project and every complication with the same level of diligence and preparation, no matter how routine things may seem on the surface.
Excavation projects are rarely simple. From underground utilities to geographical obstacles, challenges are everywhere, some in plain sight, others unforeseen. An excavation contractor’s processes need to be designed to manage every type of challenge safely and effectively, with minimal disruption.
Here are four examples of how world-class excavators like JKC build problem-solving into their processes to reduce risk and ensure the highest-quality results for complex excavation projects.
1. Taking Extra Steps to Prevent Underground Conflicts
Underground utilities aren’t always where you expect them to be so it’s worth a few extra steps to ensure that heavy equipment doesn’t get too close. Project managers can’t take anything for granted, so leveraging GPS has become a best practice. To do so, they need to walk the site, shoot GPS images of utility markers, and store the coordinates.
At the office, the site’s GPS coordinates are incorporated into topographical maps and checked against other records and plans to ensure that there are no conflicts between existing and proposed utilities. As an added step, vacuum trucks equipped with high-pressure water are used to gently expose utilities and determine their exact location and elevation. Digging by hand may also be undertaken for shallow utilities.
2. Digging Double Between Bedrock & A Hard Place
Geotechnical reports and soil borings are designed to show where the water table is, and the nature of the material you’ll be excavating. But as an experienced excavator can tell you, they don’t always represent what you find in the field. In places where shallow outcroppings of bedrock rise into an elevation where storm sewers and water mains are being installed, this complication can bring work to a crawl if a crew has to stop to jackhammer and grind their way through the bedrock.
But while the setting may be complicated, the solution is simple: running two crews, with one working ahead of the other to break up the bedrock, as the second installs the piping behind them.
3. Treading Carefully in Environmentally Sensitive Settings
Excavators need to make the extra effort on environmentally sensitive sites.
When JKC was commissioned to help build a pedestrian bridge and miles of trails over a sensitive forest preserve, the challenges were as thick as the old-growth trees and rare plants studding the landscape.
Getting several tons of heavy equipment through forest and wetlands with the lightest possible footprint required careful planning. JKC used specialized plywood matting to reduce the impact over the wetlands and tree root systems. The 8-by-16-foot mats displace the point loads of equipment to reduce the pounds per square inch across sensitive wetlands and anywhere the equipment could come within the drip line of the tree canopy.
4. Taking the High Road for More Efficient Shoreline Restoration
Shoreline restoration along Lake Michigan is a complex undertaking – beginning with access, which typically requires navigating 60-foot bluffs between the property’s edge and the lake. While other shoreline restoration companies load their equipment onto barges and work from the lake side, it’s an expensive and slow undertaking. The barges have to leave whenever the waves reach one and one-half feet or taller.
The process of creating access from the property may seem more complex and requires skilled work, but it saves property owners time and money. Bulldozers and backhoe excavators are used to cut a temporary access road through the bank, scraping away at the sides of the bluff and pushing the material ahead. It takes two to three days to build a temporary road of about 140-feet long on a 60-foot slope but, when it’s complete, the excavator can work through any weather, delivering material – and the project – in less time. unlike the barges.
The Difference the Right Excavation Partner Can Make in Tough Settings
JKC tools and processes may be complex, but our solutions are built on a simple premise: as your excavation partner, we’re invested in the success of your project. Whether you’ve got problematic ground conditions, environmental sensitivity, impossible deadlines, or all of these, you need an experienced team who can bring solutions. JKC approaches every job with a “can do, will do” mindset backed up by a highly-skilled team, state-of-the-art equipment and unmatched logistical problem-solving capabilities.
Our jobs are carefully planned to minimize risk and disruption and maximize quality, innovation and efficiency. Contact one of our excavation experts to learn more about how you can leverage our experience, processes and commitment to keep your most difficult projects on track.